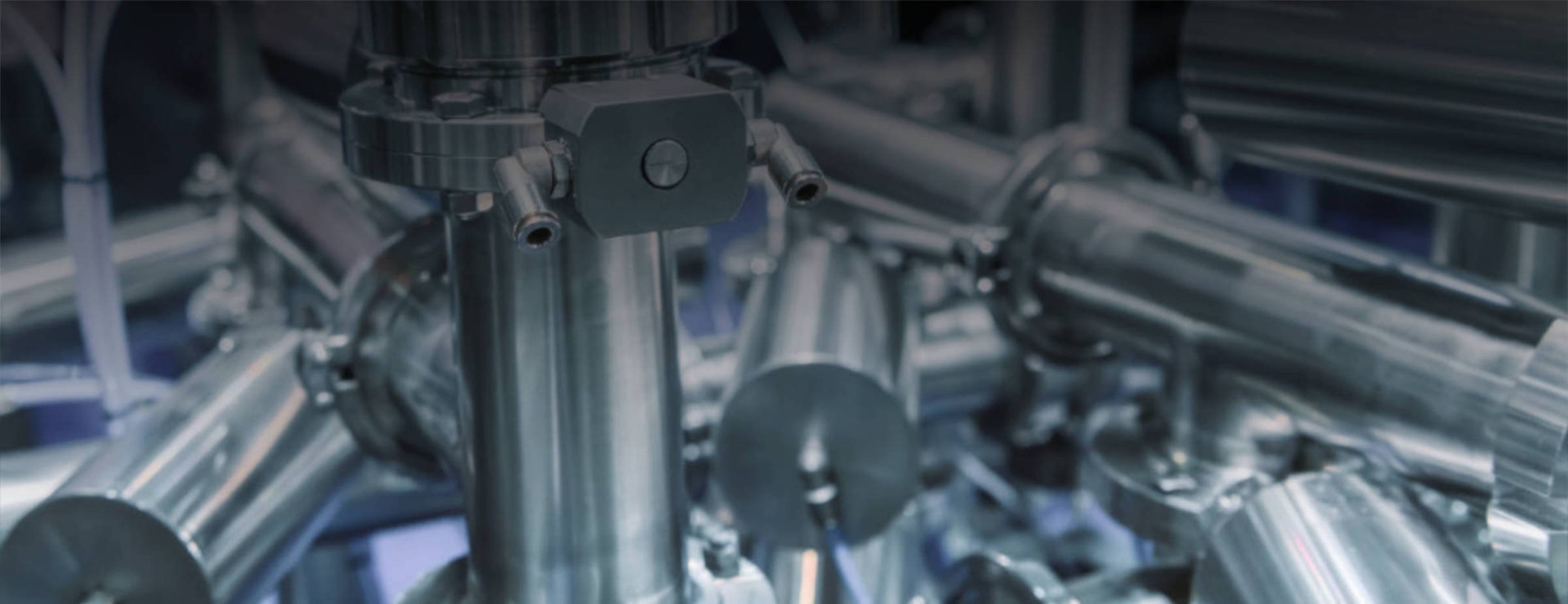
Good Manufacturing Process in Vaccine Production
27-09-2015
The production and process control of vaccines are different from those of conventional pharmaceutical products. However, the process is still based on the general principles of good manufacturing process.
Personnel
- The personnel and the manufacturer should be under the authority of someone who has been trained in the process of manufacturing biological substances.
- Personnel working in clean and aseptic areas should be free from any disease or any condition that may compromise the product’s microbiological quality.
- High standards of personal hygiene and cleanliness should be observed at all times.
- Health checks should be done to all personnel prior to employment and periodically thereafter.
- Personnel should not pass from one area to another especially if each area handles different live microorganisms or animals. This will only be allowed if there is a clearly defined process for decontamination.
- Staff who are assigned in the production should be in a separate area from those who are assigned for animal care.
- Personnel involved in this process should undergo training on good manufacturing and laboratory practices. These include bacteriology, biometry, virology, immunology, chemistry, and medicine.
- Personnel involved in the production, maintenance, testing, and animal care should receive appropriate vaccines and when appropriate, should be tested regularly for tuberculosis.
- Only those who are monitored for regular health checks should be involved in the manufacturing of BCG vaccines.
- Personnel who are involved in the production of products derived from human plasma, are recommended to be vaccinated against hepatitis B.
Premises
- There must be a separate area for manufacturing sterile biological products and for processing animal tissue and microorganisms. Each must have a separate ventilation system and staff.
- Materials used for the production of biological products such as cell banks should be stored separately. Only authorized personnel should be given access to these materials.
- Live organisms should only be handled by certain equipment that ensures cultures are kept in a pure state and free from contamination during the process.
- Products made by DNA techniques, toxoids, or bacterial extracts like killed vaccines can be dispensed in containers in the same manner as with other sterile biological products, only after inactivation and only with adequate decontamination technique.
- There should be dedicated facilities for handling spore-forming organisms like Bacillus anthracis, Clostridium botulinum, and Clostridium tetani.
- There should be dedicated facilities for the manufacture of products from human blood or plasma.
- Organisms that are considered to be pathogenic should only be handled in designated areas with negative pressure.
Production
- Cultures should be added to fermenters and other similar vessels to avoid contamination.
- If inactivation is required during the manufacturing process, certain measures should be done to avoid cross-contamination.
- There should be a clearly defined sterilization method.
Labelling
- All products should be properly labelled.
- The labels should be attached permanently to the containers regardless of their storage condition. If labelling the container is not possible, the products should be in a labelled package.
- The label should bear the following information:
- name of the product
- active ingredients and the amount of each
- batch or final lot number
- expiration date
- recommended storage condition
- handling precautions (if necessary)
- directions for use, warnings, and precautions (if necessary)
- nature and amount of substance that may give rise to adverse reactions
- name and address of the company or manufacturer responsible for this product
Quality Control
- The quality control laboratory should be a separate facility; ideally in a separate building.
- Tests that are necessary for quality control but cannot be carried out on the final product should be done during the production stage.
- There should be sufficient number of samples of both intermediate and final products to allow repetition or confirmation of batch control.
- Unlike other pharmaceutical products, which are produced using predictable chemical process, vaccine production entails a process that results to inherent variability. Hence, the process to which they are produced and quality checked is different from conventional pharmaceutical products.